Surface Finish and Texture
Many new users of small milling machines ask "what quality of surface texture can I achieve with my machine?"
Whether you are machining flat surfaces on a 2D engraver, or complex surfaces and models on 3- and 4-axis milling machines, you want them to have a predictably good surface texture.
There are several factors that affect surface quality when milling
- Machine-specific factors like flexibility, free play, backlash, spindle run-out, wear
- Cutter geometry, including flute clearance, rake angle, relief angle
- Cutter concentricity when held in the collet or chuck
- Workpiece vibration while cutting, due by workpiece flexibility and inadequate fixturing
- Spindle speed and direction
- Feed rate and depth of cut through the workpiece
- Material-specific factors such as melt-point and adhesive properties
- Cutter dimensions
- Toolpath spacing
How they relate and how to regulate them for best results on your mill
While it is not our task to provide cutting parameters for you, on all mills, for all materials, and while it is not our task to provide you with all the knowledge of an experienced, trained machinist, if you choose suitable tools, a quality mill and appropriate cutting conditions, we can give you calculation formulae. When using a ball-nose milling cutter, you need to answer these questions:
- What toolpath spacing can I use with "this tool" and still achieve "that" surface quality?
- What tool size should I use for "this" texture set by "that" toolpath spacing?
- How smooth will the surface be with "this" tool at "that" toolpath spacing?
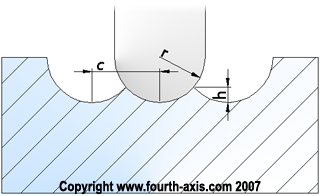
toolpath spacing:
'c' = 2√( h( 2r - h ) )
cutter radius:
'r' = (c2 + 4h2)/8h
scallop height:
'h' = r - ½√( 4r2 - c2)
Now you have scallop height, ball-nose cutter radius and toolpath spacing under your control!
CAM software packages allow you to specify the spacing of adjacent tool motions, so you can deliberately make a texture, or work very closely to make a smooth surface. There are three variables under your control - scallop height, ball-nose milling cutter size and toolpath spacing.
There are some techniques you can apply, too. Toolpaths that follow the design contours of the component look better. Toolpaths at right angles to the direction in which you may later polish, work better for polishing. An example of this polishing technique, is to make RADIAL cut strokes on a circular component that is later to be polished by spinning around its axis.
Remember that the scallop height "h" that you calculate above, is just one numeric measure of the surface finish. Multiply the "h" value (in inches) by 500,000 and you will have an approximation to the international surface roughness measure Ra in micro-inches. Multiply the "h" value (in millimeters) by 500 and you will have an approximation to the international surface roughness measure Ra in microns or micrometres. Ra was formerly known as AA (arithmetic average) or CLA (centerline average) roughness.